Description: This system uses a number of ultrasonic transducers to simply and reliably detect, locate, and quantify vorticity. In operation, an acoustic signal is propagated around a closed-loop path first in the clockwise direction and then in the counter clockwise direction. The time required for the signal to traverse the path in each direction is measured and these values are then used to directly compute the circulation contained within the closed-loop path (no correlation is required).
Potential Markets: The vortex detection system can be used to detect unwanted axial vorticity during the normal operation of wind tunnels and turbine engine test cells. The system can be used to quantify flow quality during the development of new wind tunnel facilities. The system can also be used as a research and development instrument to locate and quantify vorticity generated by a wind tunnel model.
System Description
NEAR's ultrasonic vortex detection system, as installed in an engine test cell, is described below. For this application, the ultrasonic transducers are flush-mounted into the wall of the bellmouth, as shown schematically in Figure 1 and pictorially in Figure 2. The transducers are solid-state, robust, nonintrusive to the flow, and present no FOD hazard to the engine being tested. The system initially measures the time it takes an acoustic signal to traverse clockwise and then counterclockwise around the inside of the bellmouth, as shown in the figure. If the flow velocity along the acoustic path is small compared to the speed of sound, then the difference in the two measured transit times, ΔT, can be related to the circulation, Γ, and the speed of sound, c, as ΔT = (2/c2)Γ.
An alternative configuration uses 6 transducers equally spaced around the perimeter of the bellmouth as shown in Figure 3. This method 1) reduces the chances that two counter-rotating vortices will be located within a single closed-loop path, 2) improves the signal-to-noise ratio, and 3) helps in locating the position of the vorticity. Experimental data collected in a small-scale wind tunnel are presented in Figure 4 for a NACA 0018 wing at 5° AOA. A large positive circulation from the wing tip is measured in zone 2. Similarly, a large negative circulation is measured in zone 3 from the wing root. There is very little circulation measured in zones 1 and 4. Zone 5, which incorporates the entire cross-sectional area of the tunnel, yields zero circulation due to the equal and opposite vorticity in zones 2 and 3. Numerical predictions for the vorticity generated by this wing (dashed lines) compare well to the measured values.
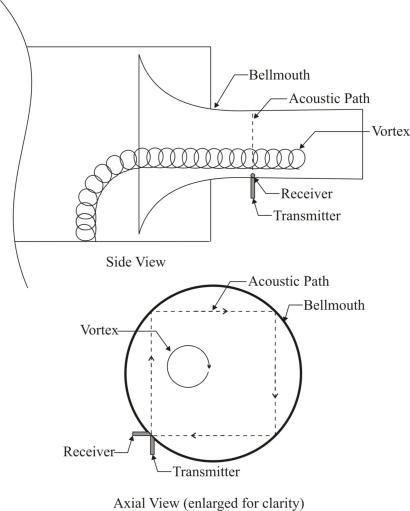
Figure 1 An ultrasonic vortex detector installed into a bellmouth, side and axial views.
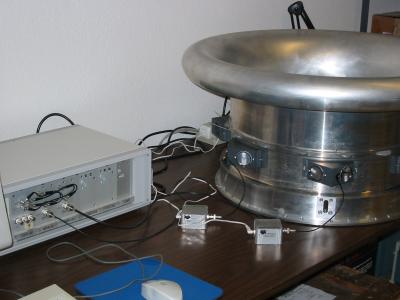
Figure 2 Photograph of NEAR's ultrasonic vortex detection system installed on a typical turbine engine bellmouth.
Figure 3 System configuration with 6 equally spaced transducers.
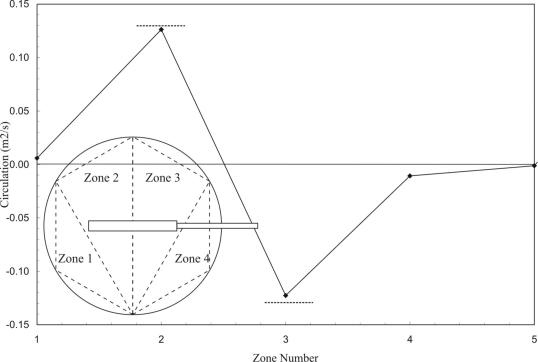
Figure 4 Experimental Data showing the measured circulation in each zone for a NACA 0018 wing at 5° AOA. Dashed lines are numerically predicted circulation values.
Ultrasonic Vortex Detection System
Innovative Solid-State All-Weather Shear Stress Transducers